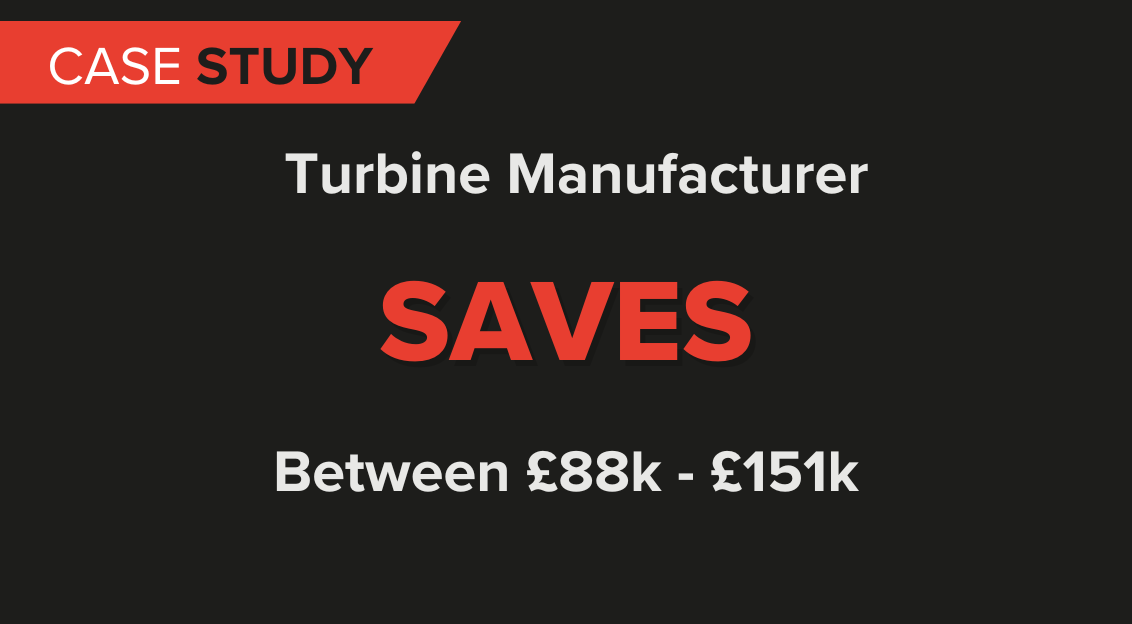
The Situation
The customer, a manufacturer of gas-path components for turbines based in Yorkshire, wanted to better understand their use of compressed air. The business approached HAYLEY DEXIS and asked us to carry out an air leak survey to help them to identify potential cost-savings. A second objective of the survey was to identify opportunities to optimise compressed air use on-site.
The Solution
A comprehensive survey was conducted to measure air leakage and calculate the financial impact. All leak points were photographed and tagged. The four compressors on-site were operating at 6.9 – 7.1 bar, costing between £88,000 and £151,000 per year to run. A recommendation was made to the customer to reduce the generated pressure to a lower level.
A further recommendation was made to replace filter elements within the compressors. Also advised was a switch to Meech 45400 blowguns, to save up to 70% of compressed air consumption.
"THE ANNUAL COST SAVING TOTALLED £28,528."
The Result
The customer took on-board all of the recommendations from the survey. The cost to repair the leaks was just £400, with the total annual cost of the leaks estimated to be around £17,500. This meant that payback on the work was achieved within just two weeks. Beyond the air leaks, the estimated cost-savings for the optimisation opportunities that the survey identified stood at £11,028. This brought the total annual cost-saving achieved to £28,528.