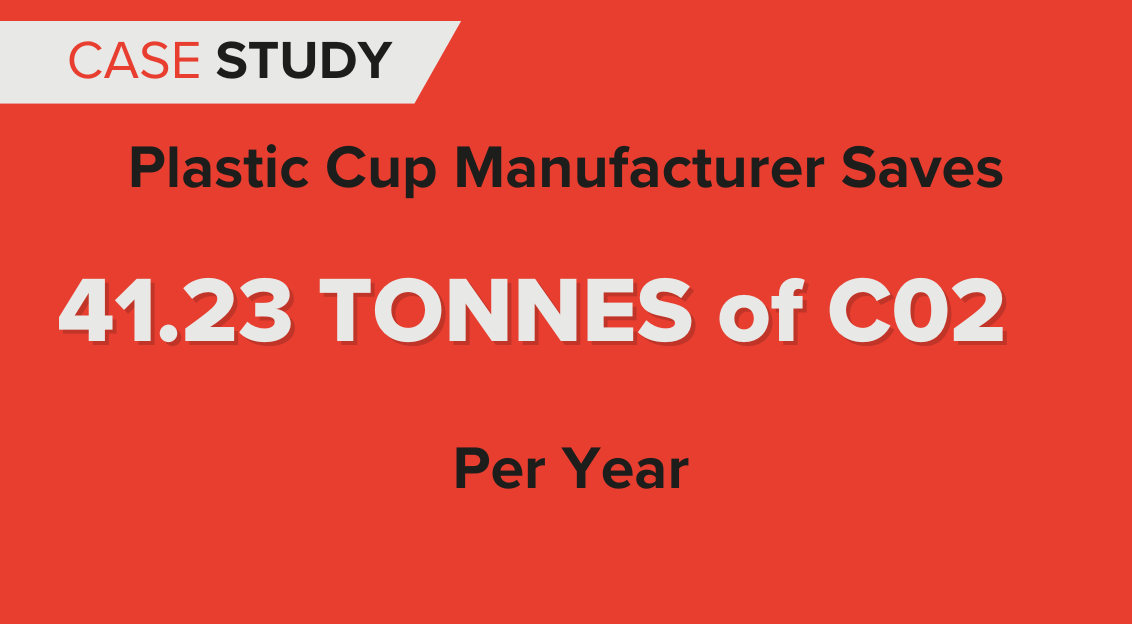
The Situation
The customer, a manufacturer of plastic caps and closures for the beverage industry, approached their local HAYLEY DEXIS branch to help them to optimise the use of pumps at their facility. A representative from the branch, along with a member of the specialist pumps team attended site to conduct a system audit. They found over fifty Grundfos multistage pumps being used for high pressure cooling purposes, some of which were up to fifteen years old.
The Solution
A trial was carried-out using a Grundfos CRiE 15 pump and a Vertical Multistage CRiE 10 pump, as an alternative option. The purpose of the trial was to assess both the flow and pressure that the system could adequately run with, and to find an accurate duty point. The customer opted for the CRIE 15 model, as it had helped to considerably reduce individual pump energy consumption during the trial. The team then worked with the customer to provide an accurate picture of energy consumption savings if the solution were to be scaled-up. Once approval was granted, a total of ten pumps were substituted.
"THE CUSTOMER’S CARBON FOOTPRINT HAS ALSO BEEN REDUCED AS A RESULT."
The Result
Following the replacement of ten pumps, the on-site consumption of electricity has been significantly reduced, leading to an annual cost-saving in excess of £6000. With this saving, the customer will achieve a total return on their investment within a little over 3 years.
The customer’s carbon footprint has also been reduced as a result, by a rate of 41.23 tonnes of CO2 per year. The new pumps have also had a positive effect on the reliability of the production line, with fewer breakdowns being reported.