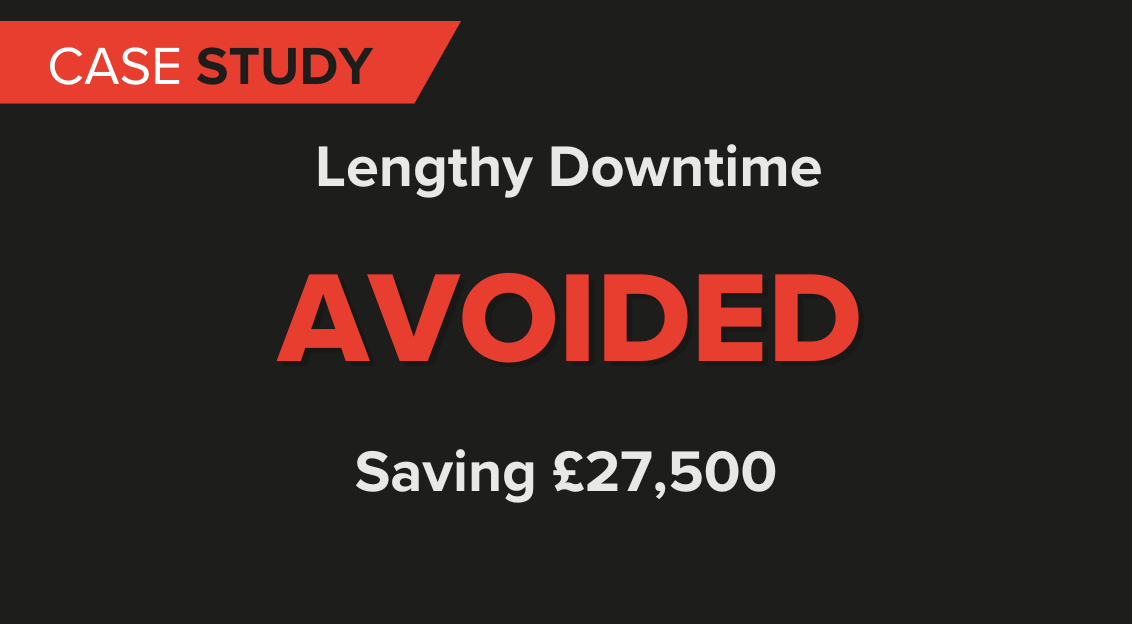
The Situation
A poultry processing facility in Norfolk contacted their local HAYLEY DEXIS team to visit site and identify motors being used to power a drum de-boner machine. During the visit, it was noted that the output shafts had been sheared off due to repeated overloading. These would need replacing urgently. The motors were also identified as OEM specials, meaning at least a two-week lead time on their replacement.
The Solution
The motors were removed by HAYLEY DEXIS and sent straight to the HAYLEY 247 DEXIS workshop in King’s Lynn. The specialist engineers within the team overhauled all three motors, treating the job as a priority given the criticality of the customer’s application. Brand-new output shafts were reverse engineered in the same workshop, manufactured from high tensile EN24t steel to prevent future shearing. The units were reassembled, cleaned, and sent back to the customer, all within twenty-four hours.
"THE NEW OUTPUT SHAFTS ARE FAR BETTER SUITED TO THE APPLICATION."
The Result
Without the electric motor overhaul and reverse engineering services delivered with such a fast turn-around, the de-boner application would have been offline for at least fourteen days. The total downtime costs calculated from the lost production stands at £27,500. The new output shafts are far better suited to the application, providing improved strength and durability. This will help to prevent future premature failures and reduce the costs and labour needed to keep the machine running effectively.