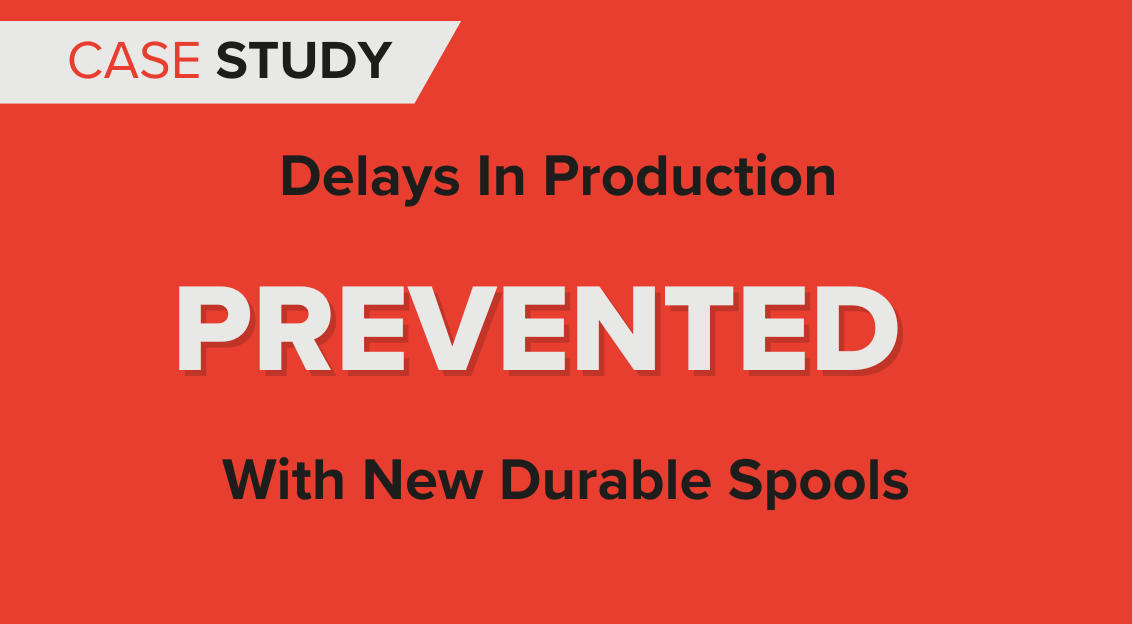
The Heading
One of the processes at the customers’ production facility, manufacturing reinforcement products for the construction sector, uses large spools to coil products ready for despatch. The spools had become severely damaged over time, with delays being caused by the constant requirement for repairs. Via HAYLEY DEXIS | Drives, HAYLEY 247 DEXIS were invited on-site to inspect the spools and recommend a solution. This included the need for drawings to be made for a redesign and some re-fabrication work to be carried-out to strengthen the spools.
The Solution
From the drawings, new material specs were sourced to include laser-cut side plates, inner and outer rolled rings, 76 x 38 PFC channels, and 50 x 25 solid bars for the drive bar component of the spools. The spools were then shipped to the HAYLEY 247 DEXIS workshop in Dudley. Arch-gouging equipment was used to remove all old sections of the spool, and prepped for re-fabrication. All materials were rolled and pieces cut to size. Mig welding was carried-out on the re-fabrication, using 1.2kg M/steel mig wire. All channels, rings, spool insides, and the centre drive bars were tacked into position, before being fully-welded.
"FEEDBACK FROM THE CUSTOMER HAS BEEN OVERWHELMINGLY POSITIVE SINCE THE NEW SPOOLS HAVE BEEN INSTALLED."
The Result
The spools are now more durable, robust, and capable of withstanding the tough operational conditions that they have to face on a daily basis. This means that the maintenance burden has been reduced significantly, cutting spend and preventing delays in production caused by downtime.
By their very design the new spools will last longer, avoiding the need for replacements to be purchased in the near future. Feedback provided by the customer has been overwhelmingly positive since the new spools have been installed at the factory.