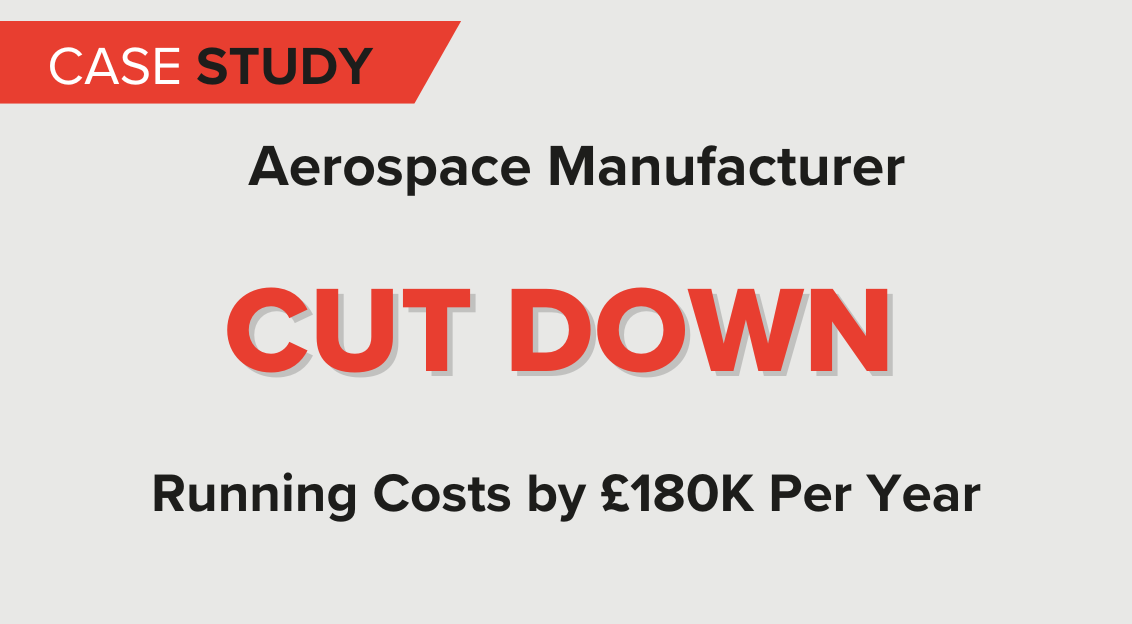
The Situation
The customer, a leading manufacturer of aerospace components, was using thirty Grundfos pumps at their facility in Scotland. The pumps were running constantly at full power, even after nozzle valves had closed with the machine’s need for fluid having passed. This was not only a waste of energy, but also resulted in a water hammer effect being created, presenting a risk to health & safety and the longevity of the system.
The Solution
HAYLEY DEXIS worked with Grundfos to conduct an ISO 14414-accredited energy check at the factory. A pump upgrade was recommended, in order to dramatically reduce energy consumption and the associated costs, as well as extend the service life of the pumps. The Grundfos CRE 32-7 AN-F-AE-HQQE was the chosen solution, as it would allow the maintenance of a constant pressure, while slowing-down to a stop as the nozzles close. The pumps would restart in a slow and controlled manner, reducing the water hammer effect and extending their service lifespan. A two-week trial period was arranged, to prove the energy and cost-saving capabilities of the new pumps.
"AN OVERALL COST-SAVING OF £180k PER YEAR HAS BEEN ACHIEVED."
The Result
The trial period was successful and the energy check findings were proven and the solution installed across the site. The wasted energy caused by the previous pumps running continually, has now been eliminated. The annual cost-saving per pump was just short of £6k, meaning an overall saving of £180k per year has been achieved. This has meant that a complete payback on the initial investment was possible in two years. As a direct result of the reduction in energy consumption, the CO2 emissions attributed to the facility have also been reduced, supporting the customers’ drive for improved environmental sustainability.