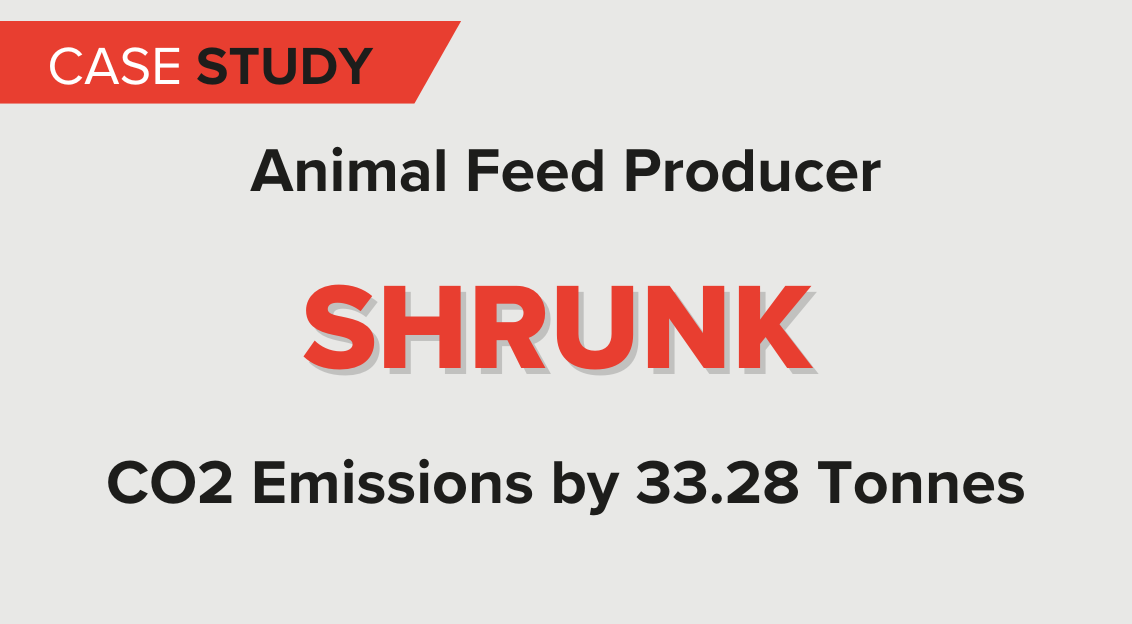
The Situation
The customer, a leading producer of animal feed, was operating two ageing Alfa Laval pumps on their soy processing line. A solution was needed to reduce the electricity costs at the plant, with the plant’s engineers also keen on improving the performance information that they currently had available to them.
The Solution
A comprehensive site survey was conducted by HAYLEY DEXIS in conjunction with Grundfos, to understand the current system. The Grundfos Multistage Variable Speed Centrifugal Pump was identified as the solution, as it is able to handle the media at the required flows and pressure. The built-in variable speed drive would use the minimum amount of energy to achieve duty, automatically switching-off when not needed. The 7.5kW motor in the current pump was working 24/7/365, even when not required to. A Grundfos Go controller was also included to enhance the monitoring of the system, by providing engineers with real-time performance data via a mobile device.
"PAYBACK TIME ON THE SOLUTION WAS JUST EIGHT MONTHS."
The Result
The substitution of the two 7.5kW gear pumps operating 24/7, for two 4kW multistage pumps operating for just 30 minutes each day has undoubtedly reduced energy consumption at the plant. This reduction has contributed to a considerable annual cost-saving of over £12k for the customer. As a result, payback time was just eight months. It is also estimated that the energy efficiency improvements made will reduce the CO2 emissions of the facility by 33.28 tonnes per year. The implementation of Grundfos Go has also enhanced the monitoring of the system.