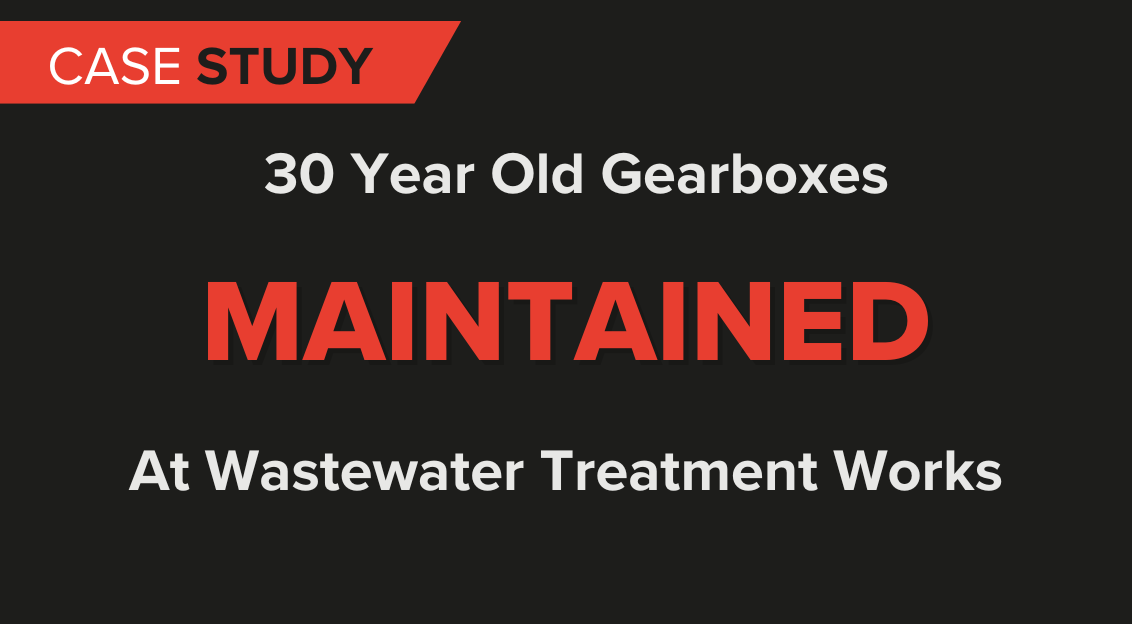
The Situation
The site was operating with an obsolete gearbox unit that had not been manufactured for 30 years. Its components, including bearings and seals, had been replaced many times and were now reaching the end of their natural lifespans. The team at HAYLEY DEXIS was asked to provide a modern solution to improve reliability and reduce operational costs.
The Solution
The solution was designed with the same dimensions as the existing unit to fit seamlessly within the existing space. The shaft dimensions on the new unit were also matched to fit the existing wheel, allowing it to continue driving the tank from the outside. The redesigned gearbox was a modern Siemens helical bevel unit with a 363:1 ratio, a six-pole electric motor, a complete base plate, a special output shaft, and two support bearings
"DOWNTIME AND MAINTENANCE COSTS HAVE BEEN REDUCED"
The Result
Thanks to the solution mirroring the dimensions of the existing unit, installation was completed quickly. This helped to keep the shutdown period required to complete the switch-over to a minimum. The new unit has significantly improved energy efficiency, reducing running costs for the customer. As a result of this, the carbon footprint of the operation has shrunk. The new unit is also capable of transmitting more power and torque than the previous gearbox. It is, therefore, able to cope with heavier loads, and will be better equipped to deal with any future increases in production. Improvements to reliability are also now being enjoyed by the customer.