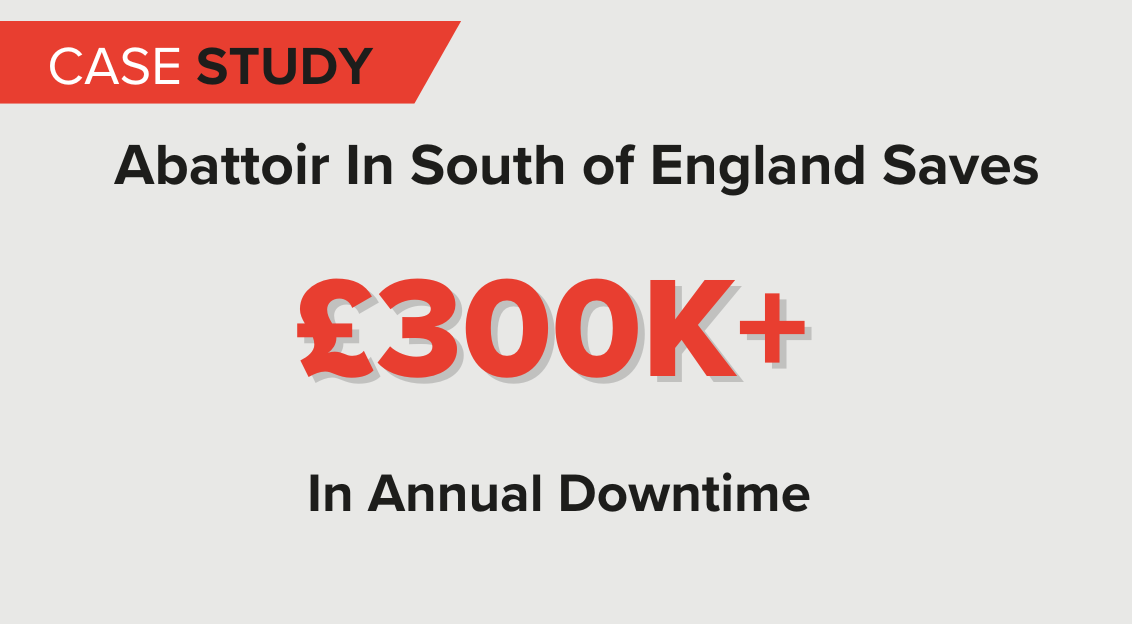
THE SITUATION
An abattoir in the South West of England had increased production over the course of the previous eighteen months, in order to keep up with surging demand. Due to an increase in production hours
required to satisfy this demand, the frequency of planned maintenance intervals had been reduced significantly. This was putting more strain than ever on critical mechanical assets in the production line. As a result, unplanned downtime was becoming more of a problem, with the hourly downtime loss rate standing at £17,000.
THE SOLUTION
After the local HAYLEY DEXIS branch was made aware of the issues, a condition-based monitoring expert from HAYLEY 247 Reliability was sent to the site to assess the customers’ assets for their criticality, and to reduce the downtime suffered on the production line. Schaeffler’s Lifetime Solutions were chosen as the best fit for the customer. This included Schaeffler’s OPTIME vibration and smart lubrication system with sensors installed in a phased approach across the facility, to reduce investment costs. As part of the service, maintenance engineers across the site were given training on the use of the OPTIME platform, and this was then fully adopted into maintenance planning procedures.
"BY ADDRESSING THE ISSUES PROACTIVELY, THE CUSTOMER AVOIDED A TOTAL FINANCIAL LOSS OF £306k THIS YEAR."
THE RESULT
Over the course of the twelve month period where OPTIME has been embraced by the customer, five motor and mechanical issues have been identified that would have previously gone undetected. Should OPTIME not have alerted the engineers to the issues before they caused a breakdown, production losses would have cost the customer in the region of £306,000. All assets now being monitored by OPTIME are also located in difficult-to-access areas, making them hard to maintain, remove, and replace, especially in a time-sensitive breakdown scenario. The customer is so pleased with the system that they are no planning to replicate its roll-out for other departments across the business.