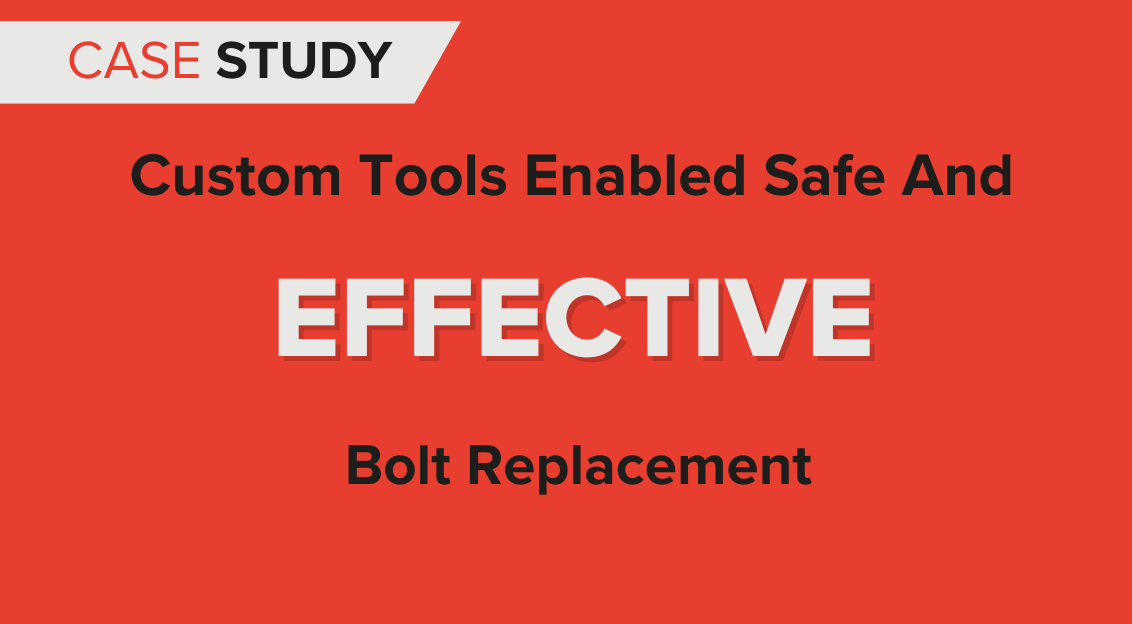
The Situation
Engineers at a train depot in the South East were risking their own safety while carrying-out the time-intensive job of removing and refitting inter-car coupler mounting bolts. The method being used involved two operators pulling on a large wrench to turn a bolt with a torque value of 1050Nm, in a restricted space underneath the train. The chance of bolt slippage and injury to operators, was substantial.
The Solution
The team from HAYLEY DEXIS | Rail worked with their torque tool partner, Norbar, to propose an entirely custom solution that would reduce the risk of injury and enable more accurate torque tightening of the critical mounting bolts. Joint visits were made to the depot, to enhance understanding of the exact requirements, before a 3D model was created to prove concept. The custom tool concept was accepted and swiftly put into production by Norbar. Once manufactured and upon delivery to the customer, HAYLEY DEXIS | Rail arranged for a member of Norbar’s technical team to visit site and conduct a training session to educate on the use of the new tool and more generally on the importance of correct torque.
"SAFETY RISKS ASSOCIATED WITH THE TASK HAVE BEEN MINIMISED, IMPROVING OPERATOR WELL-BEING."
The Result
The specially-designed tool from Norbar has made a huge difference to how the task of tightening the inter-car coupler mounting bolts is carried-out. The speed at which the job can now be completed has been increased. Not only this, but the safety risks associated with the task have been minimised, improving operator wellbeing. The tool is fully-calibrated to ensure that reliable torque is applied each and every time, within the recommended 3% tolerance range.